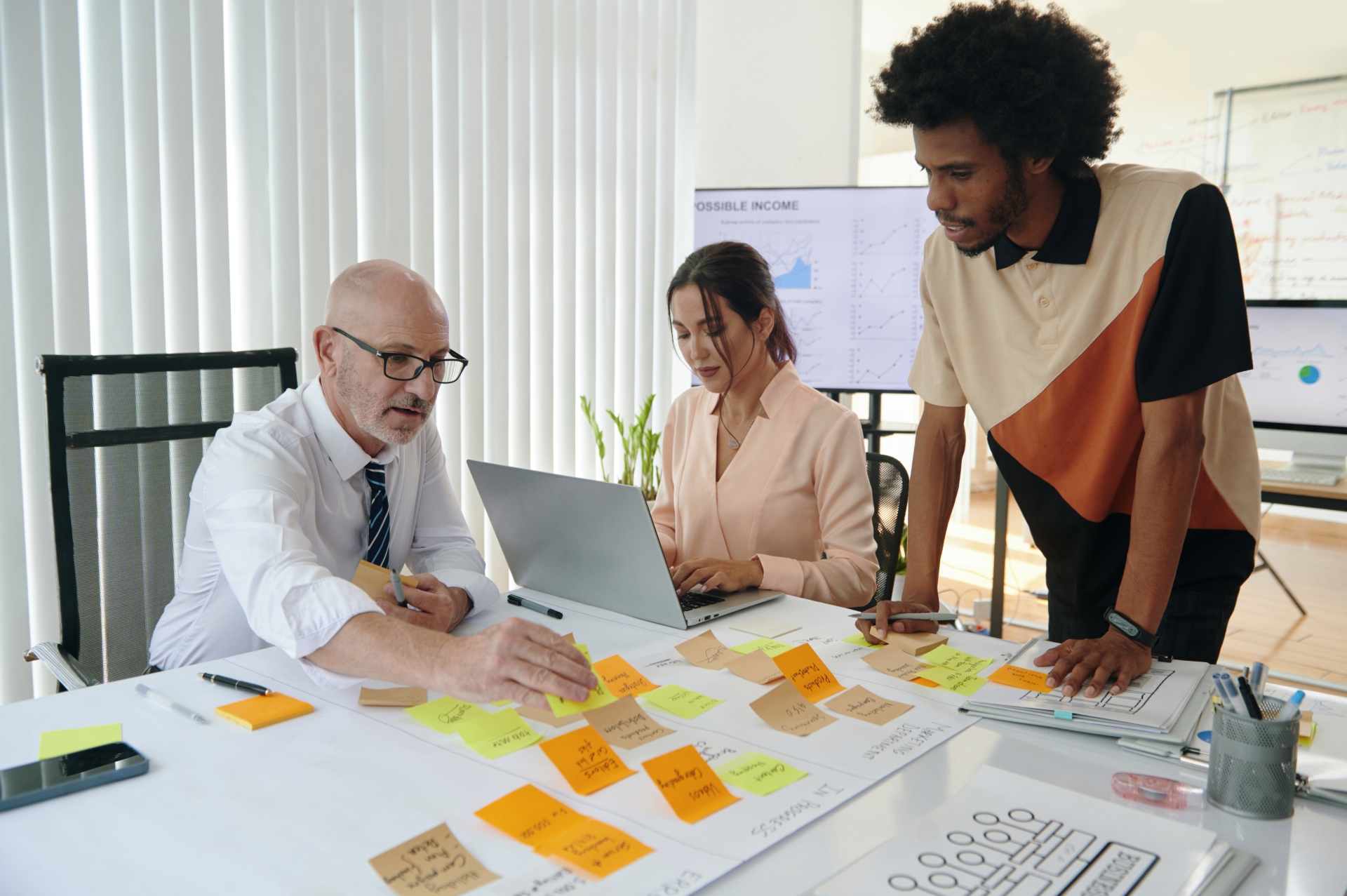
Business Process Mapping: Optimize Your Workflows
Are you struggling to understand your company’s workflows? Business process mapping provides a clear visual representation of your operations, facilitating effective improvement. Learn how this strategic approach can enhance your organization and enable digital transformation.
Summary
1- Understanding Business Process Mapping
2- Methodology for Effective Process Mapping
Understanding Business Process Mapping
Definition and Key Principles
Business process mapping involves visualizing workflows. It helps in understanding, improving, and documenting operations.
Process mapping, a website that provides information and solutions related to business process mapping—especially its definition and importance—relies on visual representations of steps, stakeholders, and resources. Tools like BPMN standardize this modeling.
Strategic Goals and Benefits
Process mapping enhances operational efficiency. It identifies bottlenecks and improves quality.
The measurable benefits of business process mapping include:
- Improved decision-making through a clear visualization of workflows and data
- Reduced bottlenecks by identifying inefficiencies in business processes
- Enhanced service quality through standardized activities and compliance with regulations
These benefits foster inter-team collaboration and align the organization’s goals with a shared vision.
Process mapping also supports digital transformation and regulatory compliance. It fits naturally into continuous improvement and compliance initiatives.
Key Components of a Process Map
Process maps use standardized symbols. BPMN provides a common visual language for all stakeholders.
Symbol Category | Symbol Type | Description and Purpose |
---|---|---|
Events | Start Event | Marks the initial entry point of a process (thin-bordered circle) |
Events | End Event | Indicates the conclusion of a process (thick-bordered circle) |
Events | Intermediate Event | Represents an event occurring during the process flow (double thin-bordered circle) |
Events | Message Event | Triggers, interrupts, or completes a process through information exchange |
Events | Timer Event | Active at a specific time or according to a defined frequency (represented by an hourglass) |
Activities | Task | Elementary unit of work in a process, non-decomposable |
Activities | Sub-process | A group of related tasks used to structure the primary process |
Gateways | Exclusive Gateway | Allows a choice between different possible paths in a process |
Gateways | Parallel Gateway | Enables the simultaneous execution of multiple paths in a process |
Connecting Objects | Sequence Flow | Solid line indicating the execution order of process elements |
Connecting Objects | Message Flow | Dotted arrow line representing communications between participants |
Artifacts | Annotation | Used to add explanations or comments to a process element |
Artifacts | Group | Graphical shape grouping of logical aspects of a process |
Process maps are structured in levels of detail—from macro-processes to specific activities—each level providing an appropriate perspective for analysis.
Integration into Business Management
Process mapping supports continuous improvement. It aligns operations with customer expectations and quality objectives.
It enhances inter-team collaboration by clarifying responsibilities. A clear view of workflows helps optimize resource usage.
Methodology for Effective Process Mapping
Key Steps of the Approach
Trust our team to assist you in the preparatory phases. Identifying the process to be mapped and involving stakeholders are the first steps. Discover our organizational and operational consulting service for your SME.
Information gathering involves analyzing workflows and identifying key stakeholders. Digital tools facilitate collaborative documentation of actual processes.
Process Modeling Techniques
A clear and transparent approach uses BPMN notation to standardize process modeling. Tools like UML also complement this methodology.
BPMN, an international standard, structures steps, events, and data objects. This modeling approach strengthens collaboration between technical and business teams.
Identifying Areas for Improvement
Key indicators reveal inefficiencies in workflows. Processing time and recurring errors guide process optimization.
Indicators that reveal opportunities for improvement in mapped processes include:
- Average processing time above industry standards
- High error rates in repetitive or manual tasks
- Frequent delays in workflows between teams
These indicators help prioritize improvement actions to manage resources effectively and boost productivity.
Prioritizing improvements requires assessing their impact on strategic objectives. Criteria such as revenue contribution and customer satisfaction guide decision-making.
Tools and Technologies for Process Mapping
Specialized Process Mapping Software
Software solutions make process mapping easier. They offer professional modeling and documentation tools.
Platforms like Lucidchart and Microsoft Visio provide advanced features for modeling processes. These tools include standard templates and collaborative capabilities.
Integrated and Collaborative Solutions
Collaborative platforms increase team engagement. They enable smooth teamwork on process maps.
Integration with existing systems ensures comprehensive process management. This enables real-time monitoring and simplifies document updates.
Criteria for Choosing the Right Tool
Several factors must be considered when selecting the right tool. Functional relevance, costs, and scalability help guide the choice.
A good cost-benefit ratio and the ability to adapt to evolving needs are essential. Ease of use and integration with current systems are key deciding factors.
Training and Team Adoption
Personalized training facilitates the adoption of tools by employees. It ensures the optimal use of process mapping features.
To ensure long-term adoption, involve teams from the beginning. Set up hands-on workshops and change management support.
Real-Life Examples and Sector Applications
Use Cases Across Industries
Business process mapping applies to various industries, including commerce and services. It highlights concrete opportunities for improvement.
Sector-specific examples include:
- In industry: mapping the supply chain to optimize production
- In commerce: standardizing prospect qualification steps in B2B sales
- In services: managing IT incidents with full traceability of customer requests
Value Stream Mapping (VSM) is a core tool in Lean Manufacturing to identify waste.
Sector-specific characteristics are apparent. The industry prioritizes cost reduction, commerce focuses on enhancing the customer experience, and services strive to optimize customer satisfaction.
Process mapping can reduce costs by 40% to 60%. 99% of Fortune 500 companies use Lucidchart to model their operations.
Business process mapping reveals optimized workflows, eliminates bottlenecks, and aligns teams around clear objectives. By adopting collaborative tools and the BPMN standard, you turn your organization into an agile and high-performing actor. Initiating this process is an investment in a strategic vision that strengthens quality, customer satisfaction, and sustainable growth at every step.
FAQ
What are the three types of quality processes?
Although the concept of “three types of quality processes” is not explicitly defined, we generally distinguish three categories of processes relevant to quality management:
- Operational processes, which relate to the creation or delivery of a product or service,
- Support processes, which provide the necessary resources,
- Management (or control) processes, which define objectives and monitor performance.
A fourth category, measurement processes, is sometimes added to assess process effectiveness and enable continuous improvement. These processes are essential for identifying deviations from objectives and implementing corrective actions in line with the Deming cycle.
How to Choose Suitable Process Mapping Software?
To select the right process mapping software, several key features should be taken into consideration. The software’s visual capabilities should make it easy to understand processes, and collaboration features are essential for allowing teams to work together effectively. Make sure the software also provides reporting and analytics tools to track progress.
Other important aspects include timeline management, the ability to define milestones and dependencies, and automation features. Finally, check whether the software integrates well with other tools you already use, and assess your team’s specific needs, your budget, and the key features that matter most to you.
How do we keep process maps up to date?
To involve teams in process mapping, it is essential to raise awareness and engage them actively. The most effective approach is to organize collaborative workshops that bring together all relevant stakeholders, including operational staff, managers, and executives. Involving employees promotes their understanding of the project and increases their commitment to change.
This participatory framework should allow everyone to speak freely and contribute to a practical and operational orientation. The goal is to solve a problem and build on what already exists. It is vital to keep the idea of customer satisfaction in mind by analyzing each step of the customer journey and considering their needs and expectations.
How do we keep process maps up to date?
To maintain up-to-date process maps, a structured and continuous approach is essential. After drawing the process maps, they should be reviewed with the process participants to ensure accuracy and completeness. Since the marketing world is constantly evolving, it is crucial to document and map all processes before implementing any changes.
The individuals who utilize these processes are the experts. It is essential to have the right level of perspective—some individuals may be too close to the processes to change them, but can still assess whether proposed changes are likely to be effective. Fully define the current state before correcting or improving the processes, ensuring you have an overall view. This leads to better-informed changes.